A Rotterdam kikötőjében működő RAMLAB és az Autodesk úttörő munkát végeznek a testre szabható additív gyártás, illetve a hibrid gyártási folyamatok terén a hajógyártásban.
A rotterdami kikötő helyszíni additív gyártólaborja (RAMLAB) és az Autodesk bemutatta az első olyan kísérleti alkatrészt, amellyel úttörő munkát végeztek az additív gyártás tengerészeti alkalmazásában. A hajócsavar készítéséhez hibrid gyártási folyamatot alkalmaztak, a huzalelektródás ívhegesztést és egy speciális 3D nyomtatási technológiát. A gyártás során ipari robotkart, illetve szubtraktív megmunkálási és csiszolási technikákat alkalmaztak.
Európa legnagyobb kikötőjeként a Hollandiában található rotterdami kikötő a világ legfontosabb áruszállítási csomópontjainak egyike. A régióban ez a kikötő biztosítja a legjobb kapcsolatot a nemzetközi kikötőkhöz, és több mint 460 millió tonnányi rakományt mozgat évente, így elengedhetetlen, hogy mind a létesítmény, mind a hajók zökkenőmentesen üzemeljenek.
Jelenleg, ha egy hajó úgy érkezik a kikötőbe, hogy alkatrészcserére – például egy hajócsavarra – van szüksége, a rendelés és szállítás heteket vagy hónapokat is igénybe vehet, a várakozás pedig eurómilliókba kerül a vállalatoknak. Az ilyen nagyméretű alkatrészek tárolása és raktározása sem olcsó mulatság

A kikötő ezt a kihívást úgy oldaná meg, hogy nyitott egy helyszíni létesítményt, az innovatív RAMLAB-ot, amelyben hattengelyes robotkarokkal végezhető el a nagyméretű fémalkatrészek additív gyártása. A RAMLAB csapata hardver- és szoftverpartnerek, akadémiai és tanúsító intézmények, valamint a legnagyobb hajózási vállalatok hálózatával működik együtt, hogy segítsen a világ legintelligensebb kikötőjévé válni.
Az Autodesk, a RAMLAB fő szoftverpartnerként kulcsszerepet játszott az innovatív hibrid gyártási folyamatok fejlesztésében. Ezzel a módszerrel a RAMLAB hatékonyabb gyártást alakíthat ki. A hajóalkatrészek 3D nyomtatása, majd a darabok hagyományos CNC-marási és csiszolási módszerekkel való készre munkálása, a korábbi hetek helyett napok alatt megtörténhet, így a pontosság és a teljesítmény feláldozása nélkül takaríthatnak meg időt és pénzt.
„A Rotterdam kikötőjében működő RAMLAB kezdeményezése kiváló példája annak, hogyan változtat meg az ipari additív gyártás egy teljes iparágat – magyarázza Steve Hobbs, az Autodesk CAM és hibrid gyártási folyamatok részlegének alelnöke. – A cserealkatrészek igény szerinti, hibrid gyártásának képessége nagy szerepet fog játszani abban, hogy csökkenteni lehessen mindazt a kárba ment időt és a tetemes költségeket, amelyek a hajóalkatrészek sérülése miatt keletkeznek az egész hajózási ágazatban. Óriási örömünkre szolgál, hogy a tengerészet kulcsszereplőivel dolgozhatunk együtt azon, hogy az alkotás jövőjét ezzel a kézzelfogható példával valóra váltsuk.”
„A RAMLAB-nál végzett munkától a csoport azt reméli, hogy felgyorsítja a hibrid gyártási folyamatok több iparágra kiterjedő bevezetését is, amellyel igény szerint nagyméretű alkatrészek készíthetők – mondja Vincent Wegener, a RAMLAB ügyvezető igazgatója. – Célunk, hogy a rotterdami kikötőt ne csak Európa egyik fontos átjárójává tegyük, hanem az új gyártási módszerek fejlesztésében is vezető szerepet töltsön be. Az Autodesk kulcsfontosságú partner számunkra, mivel komoly szakértelemmel rendelkezik arról, hogyan oldhatjuk meg a tervezést és gyártást mind a legújabb additív gyártási technikák, mind a hagyományosabb CNC- és megmunkálási módszerek alkalmazásával.”
A RAMLAB-nál végzett helyszíni munkákon túl az Autodesk azzal is támogatást nyújtott a RAMLAB-nak, hogy hozzáférést biztosított számára a Birminghamben működő Advanced Manufacturing Facility (AMF) létesítményhez, így a csapat tagjai új tervezési és gyártási koncepciókkal ismerkedhettek meg.
A két szervezet többek között a következő tevékenységeket végzi közösen:
- Az alkatrészek terveinek elemzése után megvizsgálják, ilyen gyártási lehetőségeket tesz lehetővé az additív gyártás.
- Előkészítik az alkatrészeket a gyártáshoz, és előformákat készítenek.
- A nagyobb méret okozta torzulások, maradó feszültségek, geometriai tűrések figyelembevételével felépítik ezeket az alkatrészeket.
- Utókezelési technikák alkalmazásával megismételhető és megbízható módon alakítják ki az alkatrészek végleges formáját.
Az alkotás jövőjével kapcsolatos korlátok felszámolását célzó Autodesk technológiai központok globális hálózatában működő Birmingham AMF részéről Kevin Hamilton a projekt műszaki kapcsolattartója szerint az együttműködés a RAMLAB-bal ugrásszerű előrelépést jelent a hibrid gyártási folyamatok terén:
„Az additív gyártást valóban ipari léptékűvé tettük. Mostanáig sok 3D nyomtatás a kis alkatrészekre korlátozódott. De a technológia – mind a szoftver, mind a hardver – már készen áll a nagyobb alkatrészekre is, és mi megragadjuk a lehetőséget, hogy megmutassuk a világnak, mi mindent tesz lehetővé az innovatív gondolkodás.”
Forrás: Autodesk blog
Kapcsolattartó:
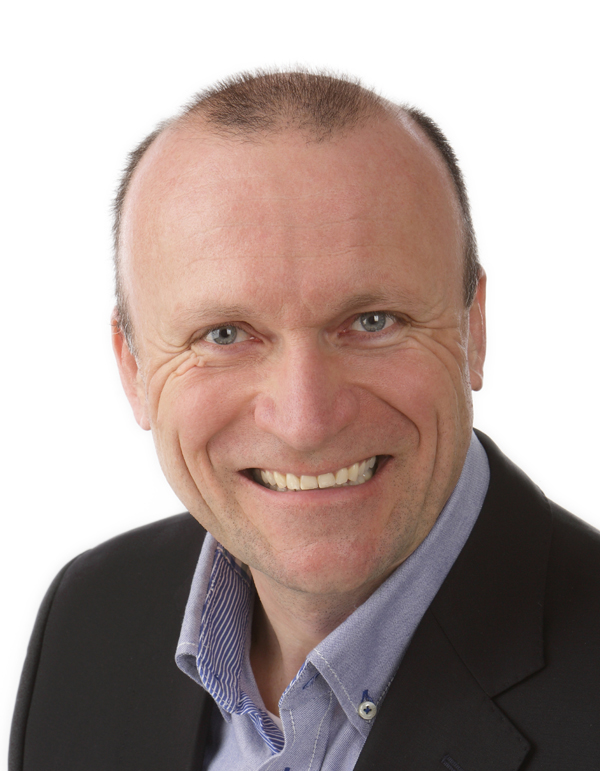